Six Pillars of Lifecycle Refrigerant Management
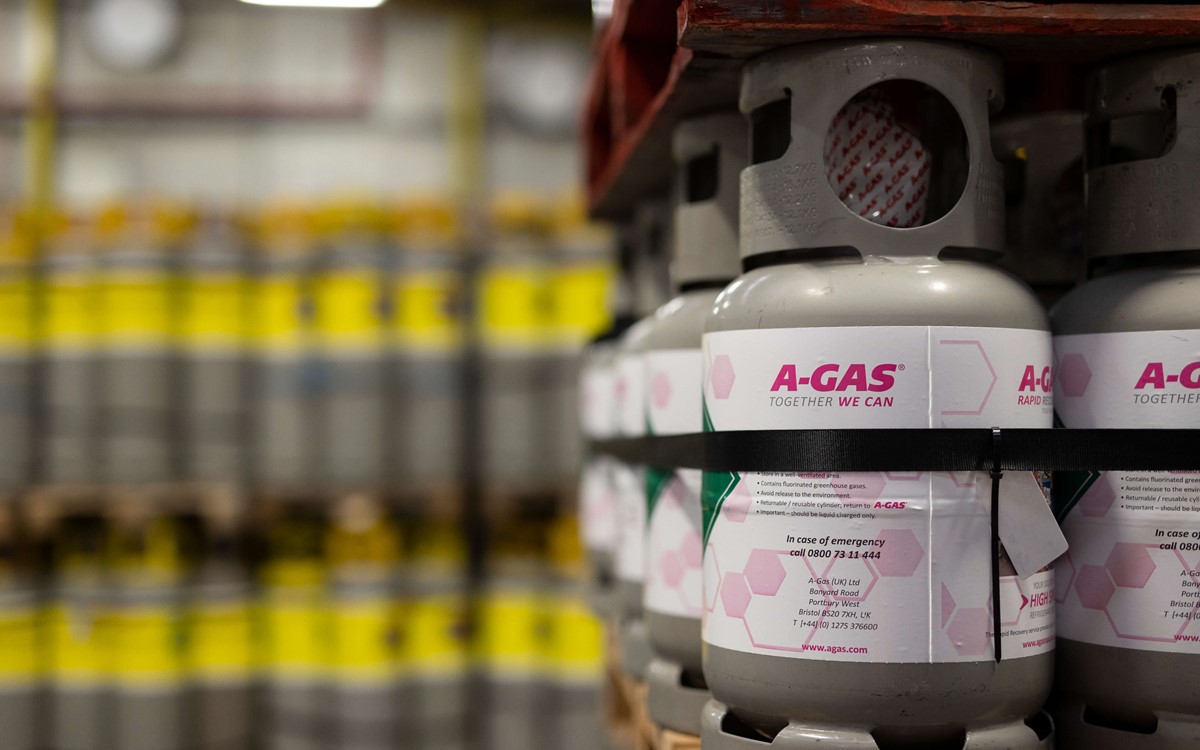
A-Gas Group Sustainability Director, Ken Logan, explains why Lifecycle Refrigerant Management will play an important role on the road to net-zero.
There are approximately five billion refrigeration, air conditioning, and heat pump systems in operation globally. Over the years, as environmental legislation has been adopted, the type and make up of refrigerants used has changed.
From CFCs and HCFCs to HFCs, HFOs, and natural refrigerants, the gases in use have changed to reduce the impact on our natural environment. Lower Global Warming Potential (GWP) refrigerants continue to be developed as we look to build a more sustainable future.
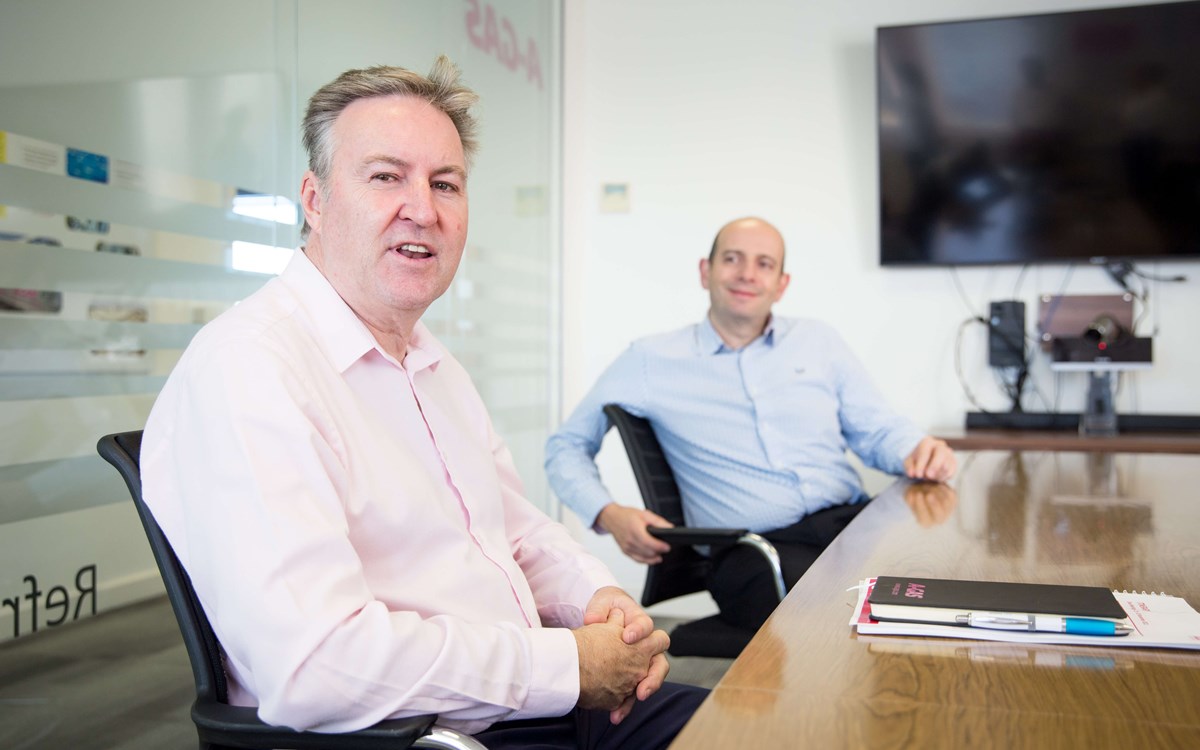
But relying on the development and use of lower GWP gases alone is not enough to reduce emissions globally. It is estimated that there are 90 billion tons of CO2-e emissions requiring abatement within the existing installed bank of Ozone Depleting Substances and HFC refrigerants. In anybody’s book that is a vast amount of potential emissions. If these legacy refrigerants are not recovered, and then reclaimed or disposed of correctly, much of the great work of the Montreal Protocol to protect the ozone layer and reduce greenhouse gas emissions will suffer.
Used refrigerant released into the atmosphere is a significant contributor in the acceleration of global warming. According to COPA (Climate and Ozone Protection Alliance), the yearly global emissions of Ozone Depleting Substances and HFCs are the equivalent of 1.5 gigatons of CO2-e—that is the same as the emission released by 441 coal-fuelled power stations.
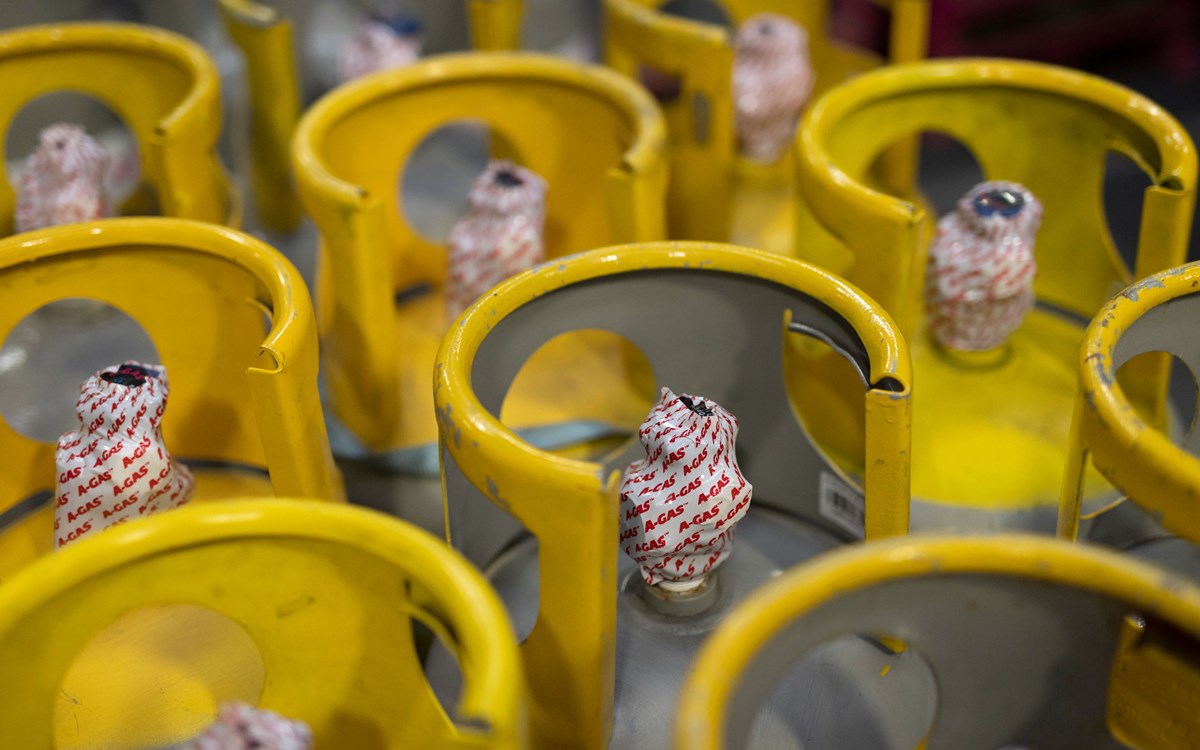
It is clear that reducing leakage and recovering refrigerants for future re-use has a far greater impact on our climate than the adoption of lower GWP refrigerants alone. Where there are no further uses for recovered gases they should be destroyed of by the most efficient and effective means possible.
Reclaimed refrigerant sent to A-Gas’ reprocessing plants undergoes chemical analysis, is cleaned of contaminants, and goes through our reclamation and separation plant, creating a product that matches that of virgin refrigerant specification. This refrigerant becomes a fully reclaimed product and is returned to the market in line with the AHRI 700 standard, replacing the need for virgin production.
Where reclamation of used gas is no longer possible or where gas has no further use, A-Gas will dispose of the material responsibility using certified and licensed disposal technologies.
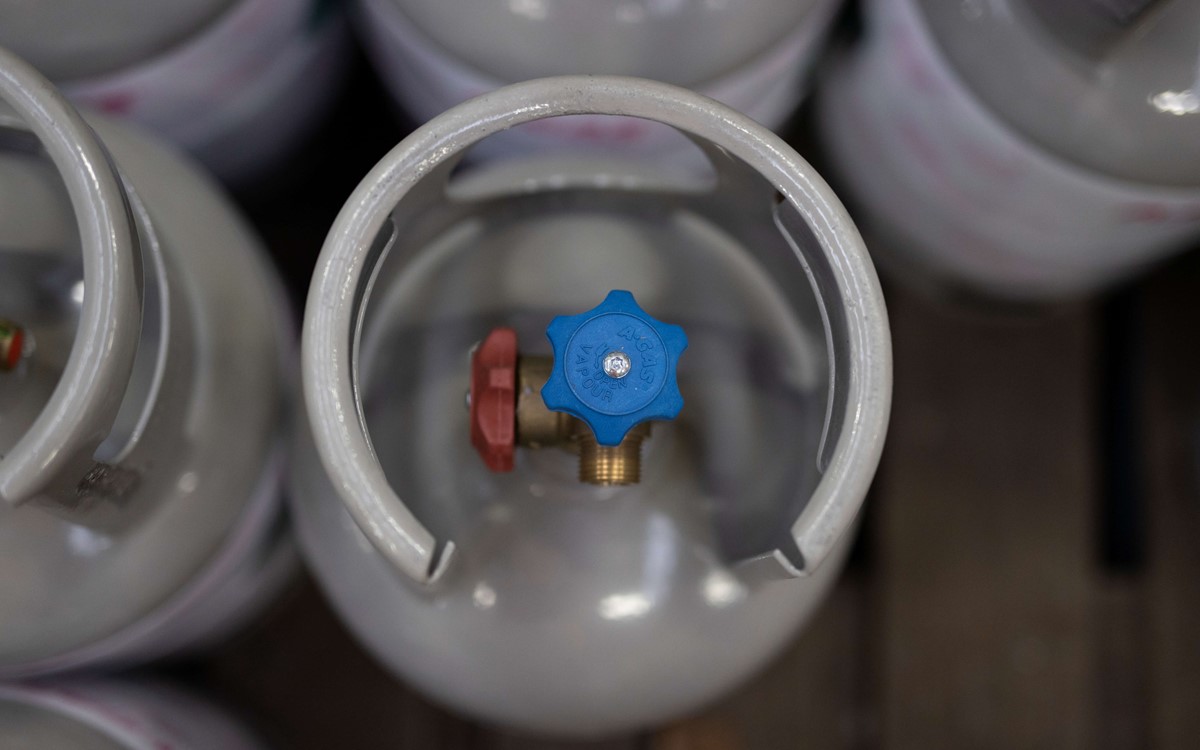
Lifecycle Refrigerant Management (LRM) is an effective and deliverable circular economy solution on the journey to net-zero. It forces us to seek greater efficiencies and make better use of what we already have. Adopting the practices of Lifecycle Refrigerant Management is key if our industry is to overcome the hurdles on the road to net-zero.
Lifecycle Refrigerant Management works in harmony with the Montreal Protocol and helps us achieve our goals faster. It goes beyond the supply of refrigerants, focusing on saving emissions and preventing the need for the production of virgin refrigerant.
According to industry experts, there are six pillars of Lifecycle Refrigerant Management that we need to be aware of and adopt:
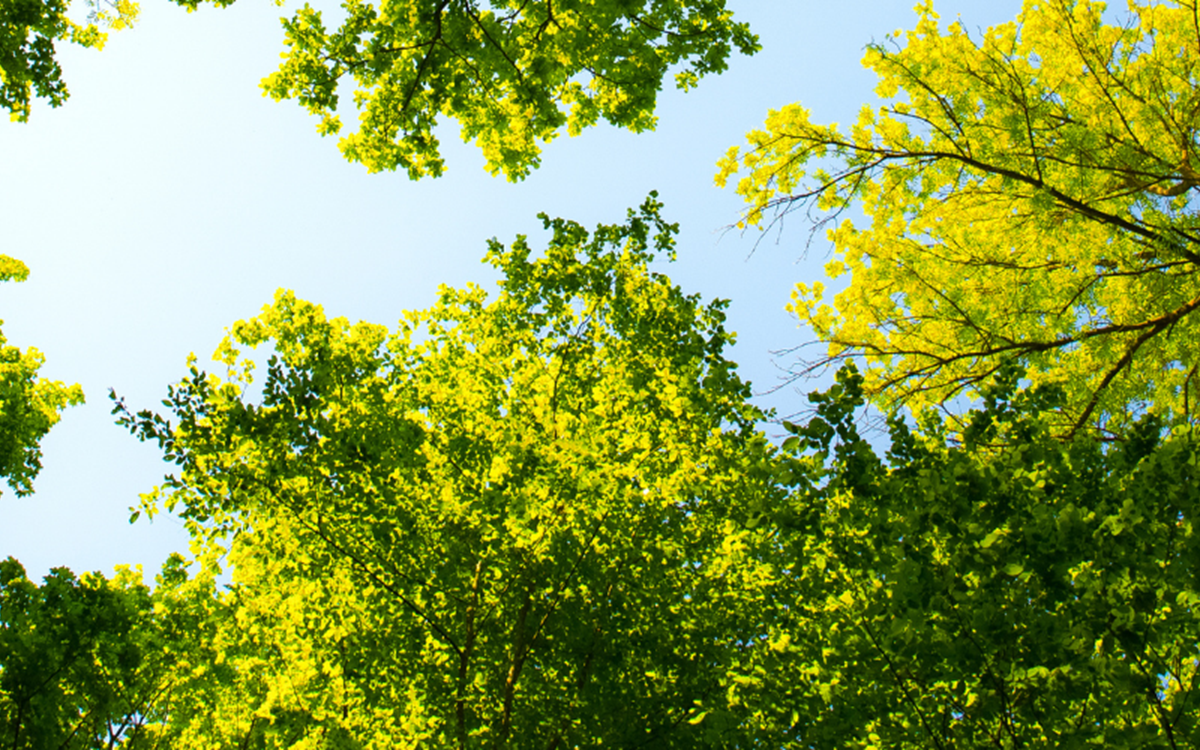
Enhanced Product Stewardship
Responsibility for environmental management of refrigerants needs to sit higher up the supply chain. Programs to help gas producers and equipment manufacturers to provide the building blocks for economically and technically feasible LRM are essential.
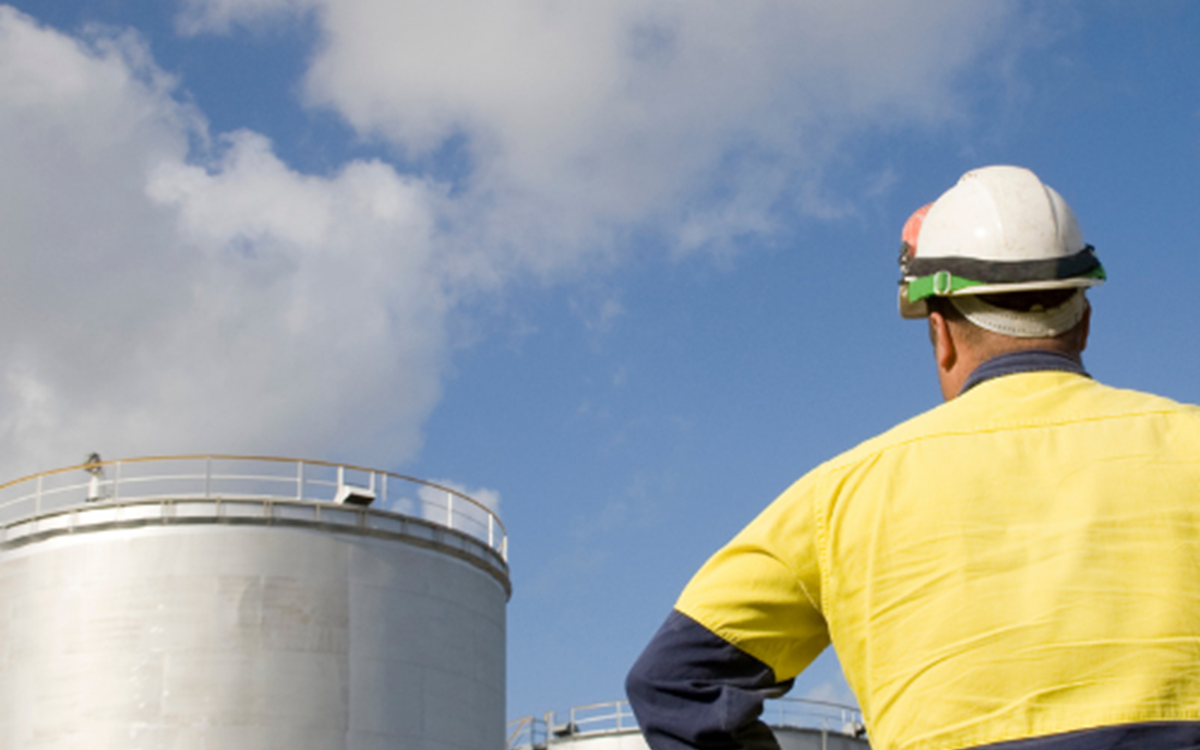
Increase Refrigerant Recovery, Reclamation & Re-Use
There should be more incentives to encourage the recovery, reclamation, and re-use of refrigerants. Encouraging the industry to make the most of the gases we already have is a founding principle of the circular economy. Reclamation relies on refrigerant recovery for a steady supply of product so emphasis must be placed on making that recovery easy and economical.
A-Gas Rapid Recovery®, the EPA- compliant on-site recovery service, is a good example of how having the right equipment can make a difference. Here, the ease with which the refrigerants are removed is made possible by our mobile A-Gas Rapid Recovery teams.
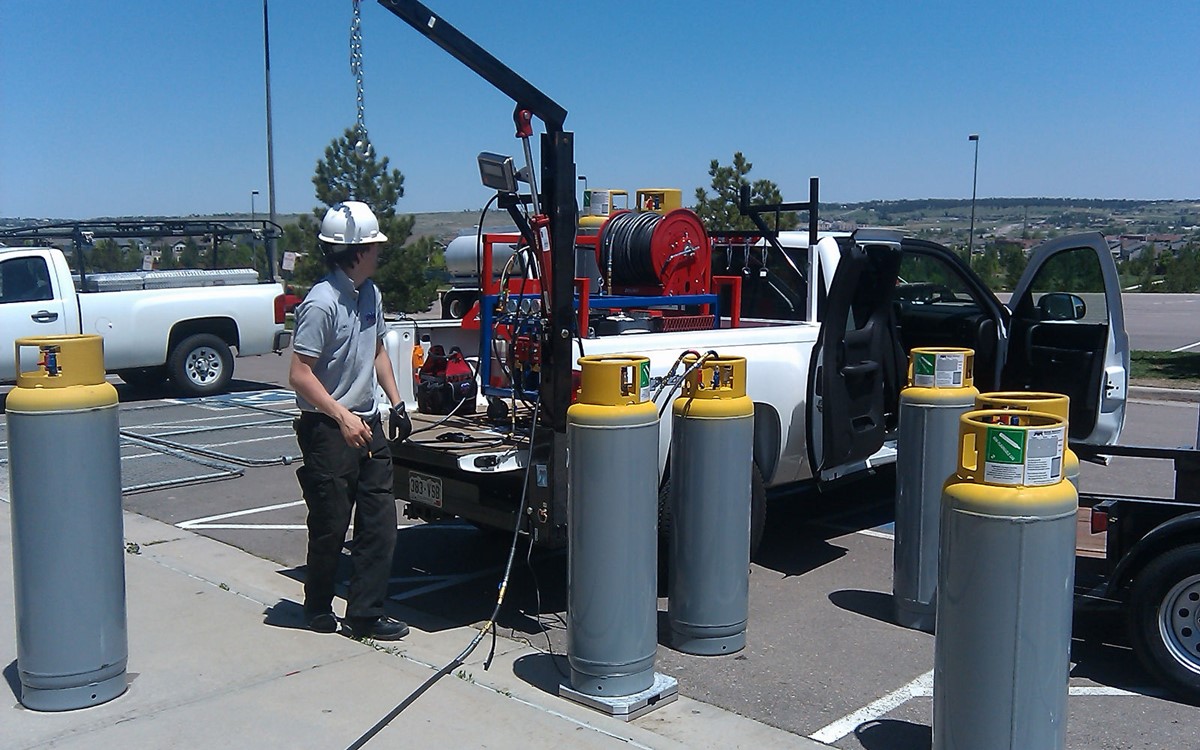
Leak Reduction
Improved maintenance and leak reduction make a significant difference as we look to reduce emissions and global warming. Targeting low leak rates is a high priority for LRM because they lead to large climate benefits at a low cost. Tools like Trace-A-Gas® from A-Gas, a five percent hydrogen and 95 percent nitrogen mixture which is non-flammable, non-toxic, and safe for the environment, can help in locating even the smallest of leaks.
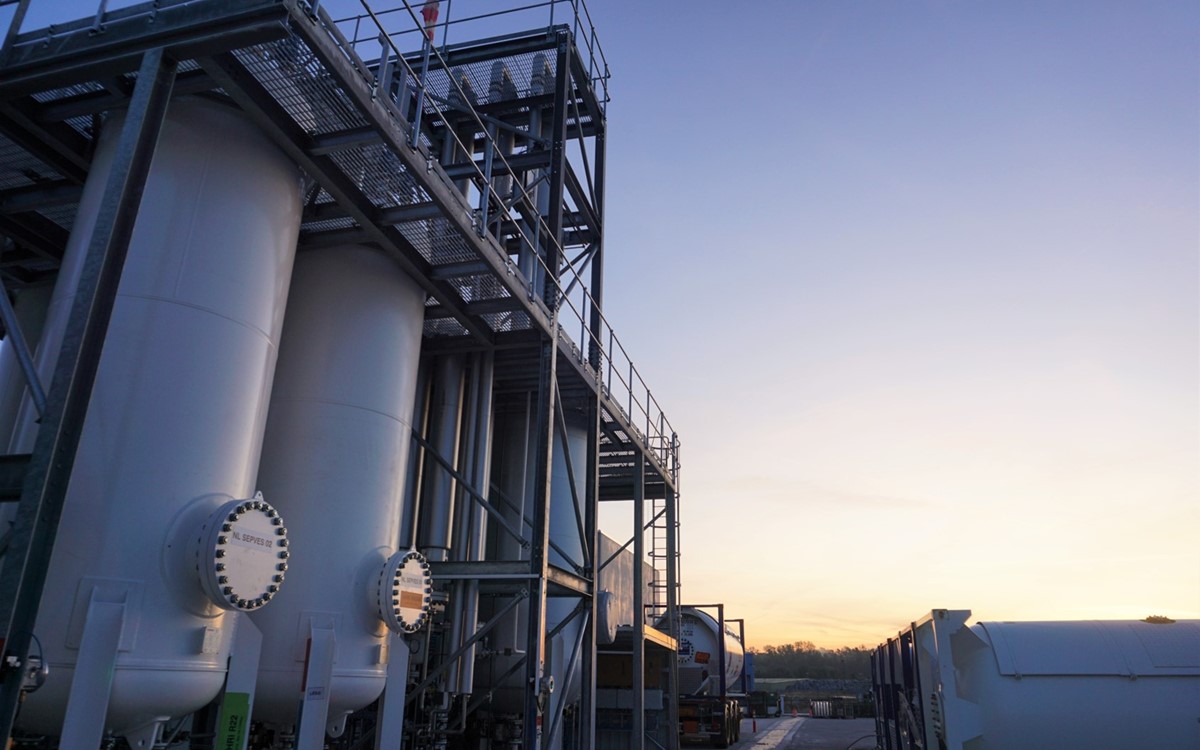
Stakeholders in the industry must continue to report improper LRM practices in the field, including violations of existing laws regarding refrigerant management. Stricter enforcement of the law and increased reporting of these activities is a must.
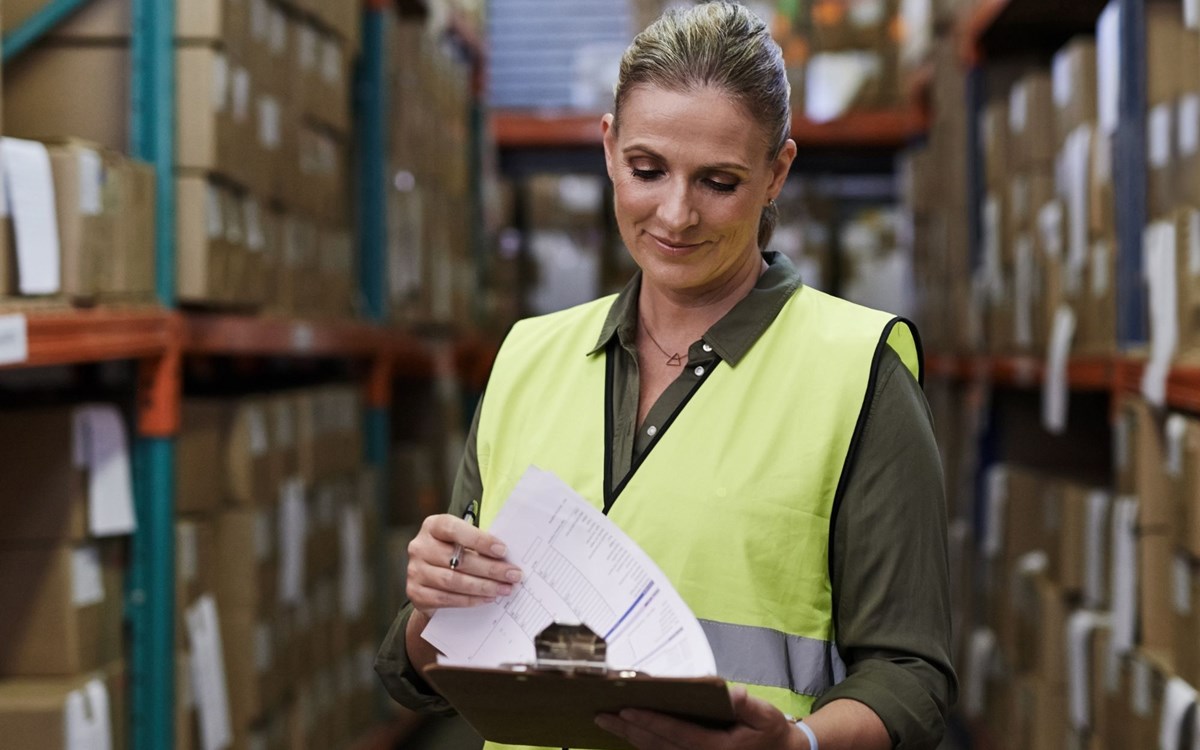
Workforce Development
More training is required if we are to ensure that the industry workforce is able to handle the demands of new lower GWP refrigerants, improved leak detection, the re-use of gases, and safe environmental disposal when end of life is reached. Equipment and refrigerants are changing at a rapid rate and we need a skilled workforce to handle this. The industry is already looking at ways to share knowledge and improve the skills base but there is much work to do here.
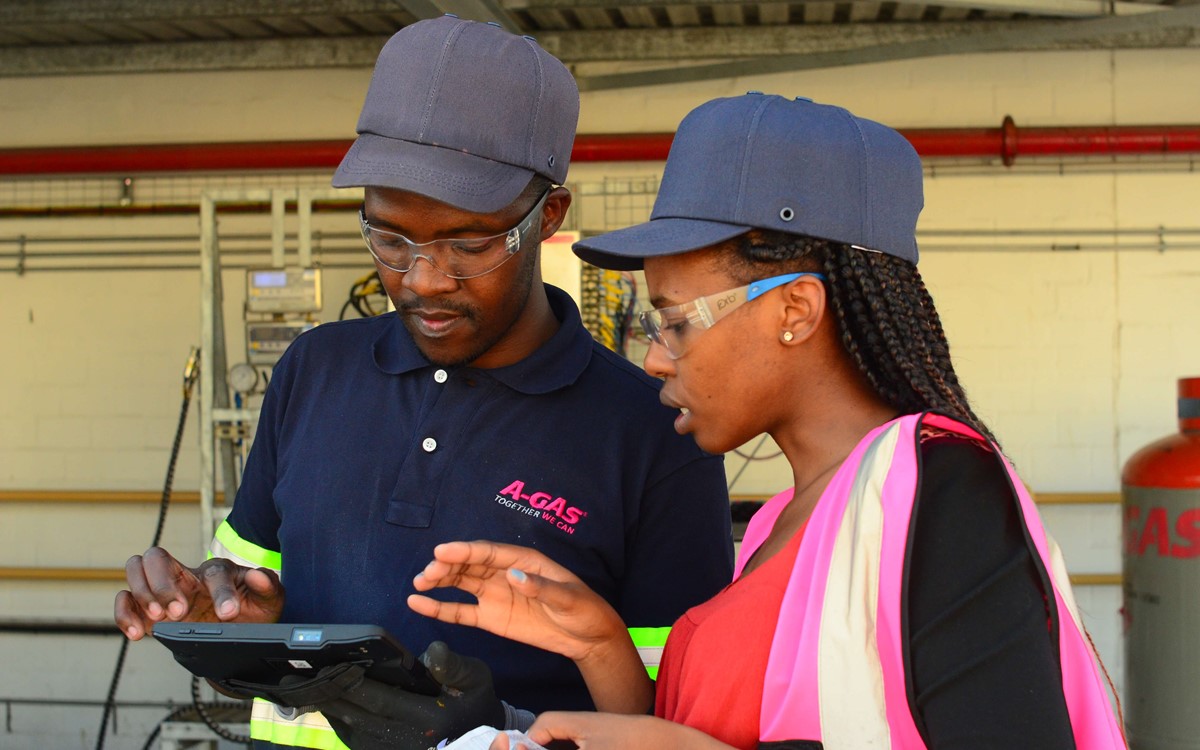
Installation & Servicing
Installation is the starting point of the equipment’s life. LRM cannot be achieved without proper installation and verification. Servicing practices, such as the widespread technique of topping up leaky systems without repairing the underlying leaks, should be discouraged and avoided whenever possible.
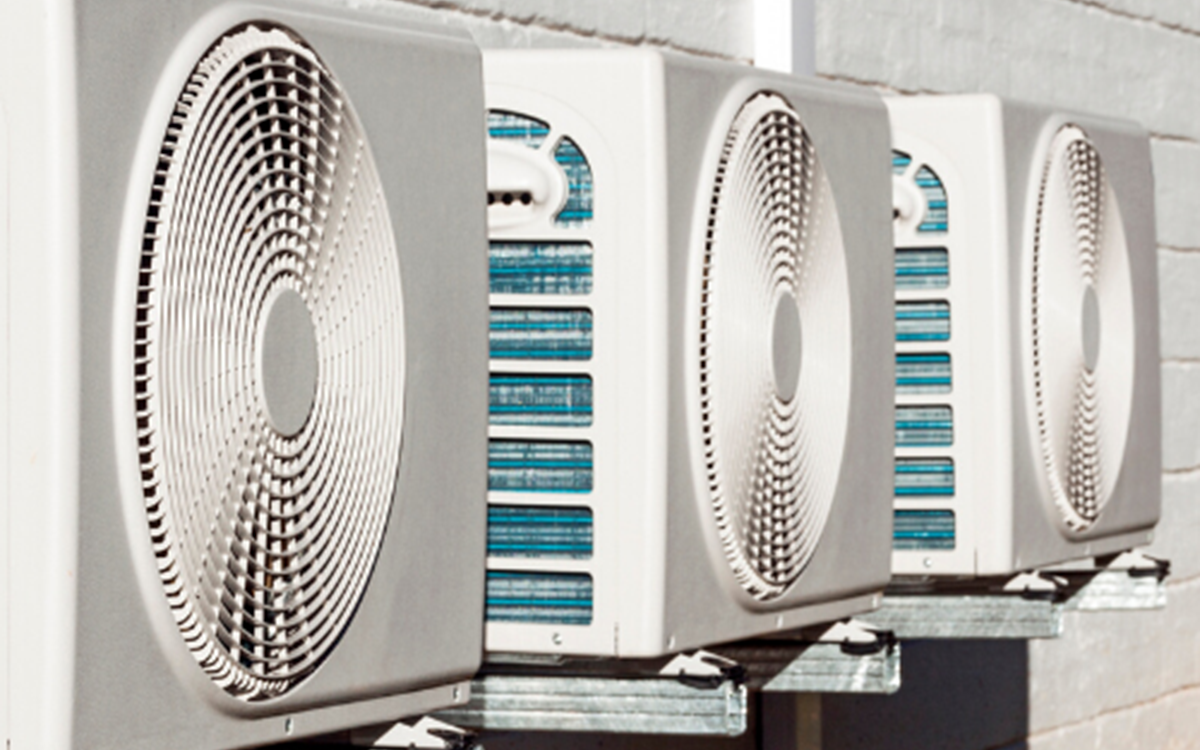
The Six Pillars of Lifecycle Refrigerant Management can help guide the industry globally on the long journey to net-zero. As part of this, it is imperative that we capture and correctly process all the legacy refrigerants that are in use—otherwise much of the benefits generated by the Montreal Protocol will suffer.
Around the world, no pound of refrigerant should be allowed to go to the atmosphere. As an industry, we need to do all we can to achieve this. Our climate goals are ambitious, but together, we can.
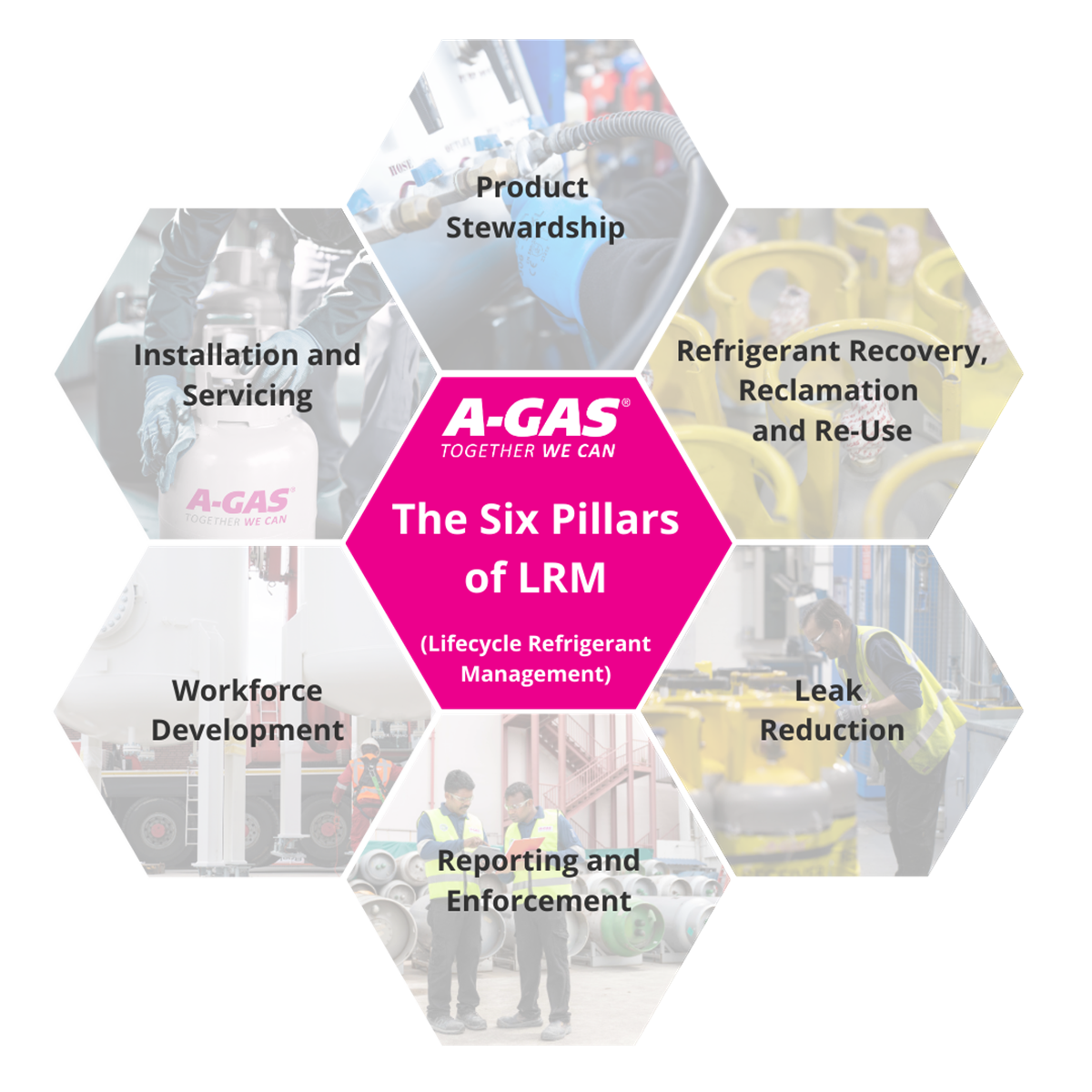
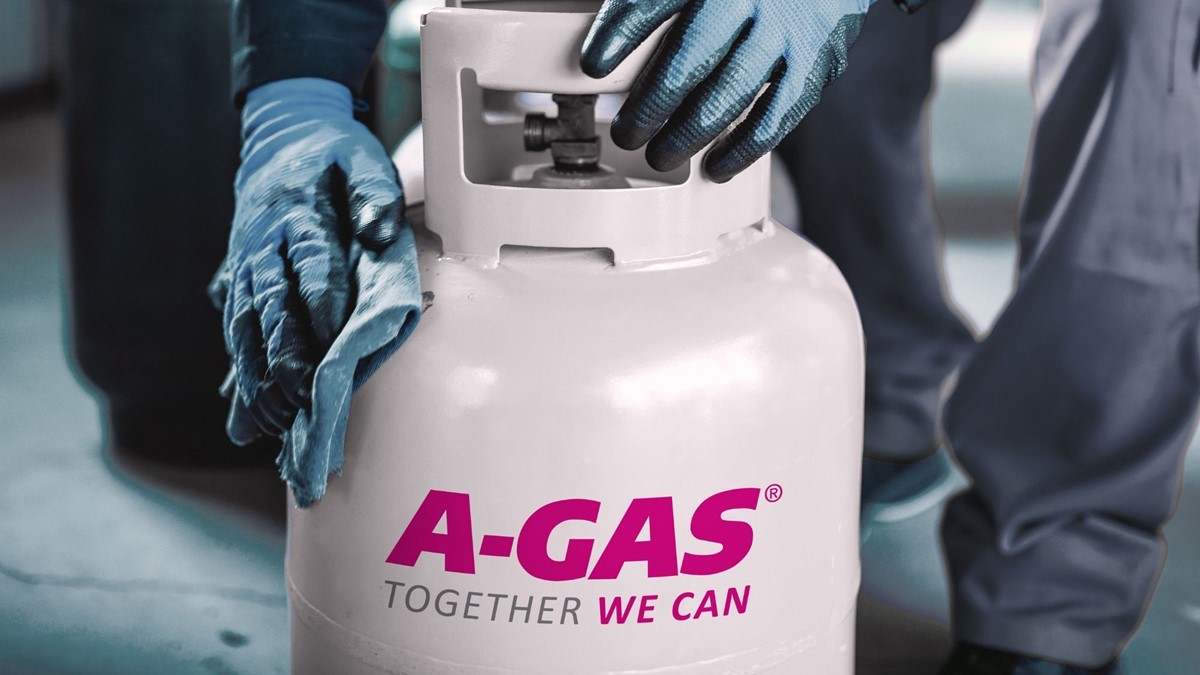