A-Gas Rapid Recovery Operations Manager, Jake Matthews, explains how his teams recover refrigerant and help return it to market.
No day is the same for our A-Gas Rapid Recovery teams. The growing demand to recover refrigerants and use them again means that our jobs are always presenting new challenges.
Reclaimed gases are quota free and refrigerants saved from disposal and returned to the market also reduce raw material usage, energy consumption and unnecessary transport normally associated with virgin production. All of this fits in well with the F-Gas Regulations and low carbon business frameworks.
At Rapid Recovery, we operate as single, two or three-man teams depending on the size of the job. We travel anywhere in the UK to recover refrigerants, as we know how important both recovery and reclamation are to preventing ozone depleting gases escaping into the atmosphere. Supermarkets, data centres and buildings with large Variable Refrigerant Flow (VRF) air conditioning installations feature among the jobs we tackle.
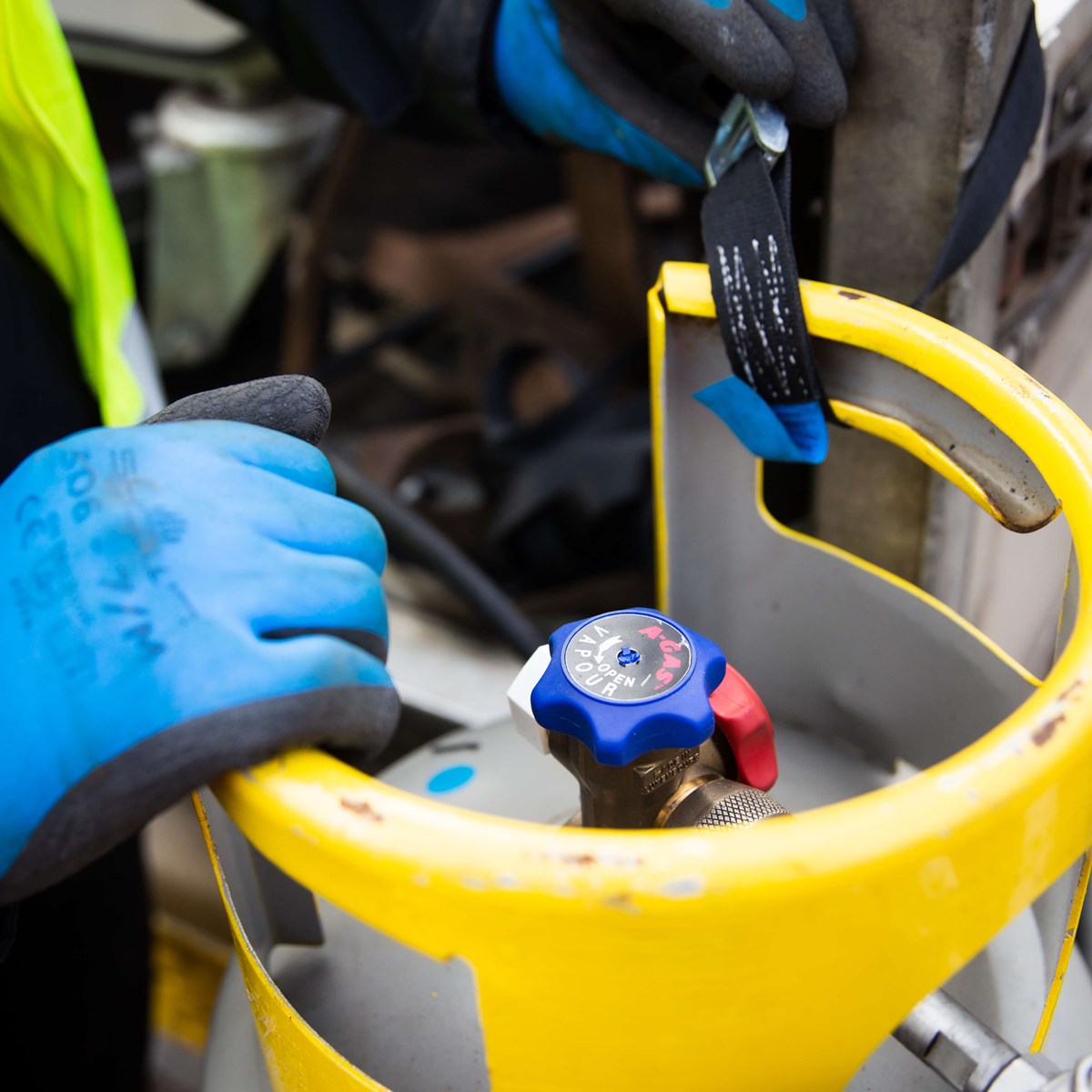
Typically, you will see Rapid Recovery personnel working high up on the roof of a supermarket or office block. The ease and speed of Rapid Recovery really does make a difference. Using a Rapid Recovery team can be up to ten times quicker than the contractor removing the gases themselves.
On the road, it’s more than likely to be a retrofit job we tackle, where the end user is switching to a lower Ozone Depleting Substance (ODS) and wants the high Global Warming Potential (GWP) refrigerant removed and available for re-use.
Supermarkets now want to switch to zero or lower GWP refrigerants. They cannot afford much downtime on the hard-working fridges and freezes they use in store.
We are often called in to remove R404 or R407 to replace with R448A or R449A. Our help allows on-site engineers get on with other key jobs, keeping downtime to a minimum is crucial.
We arrive on site in a flat-bed truck or van, depending on the nature of the job, with the Rapid Recovery equipment on board and all the cylinders, hoses and adapters needed. Ideally, we will recover directly from the vehicle but we also have a mounted crane available so we can move the mobile recovery machines and use them around the site.
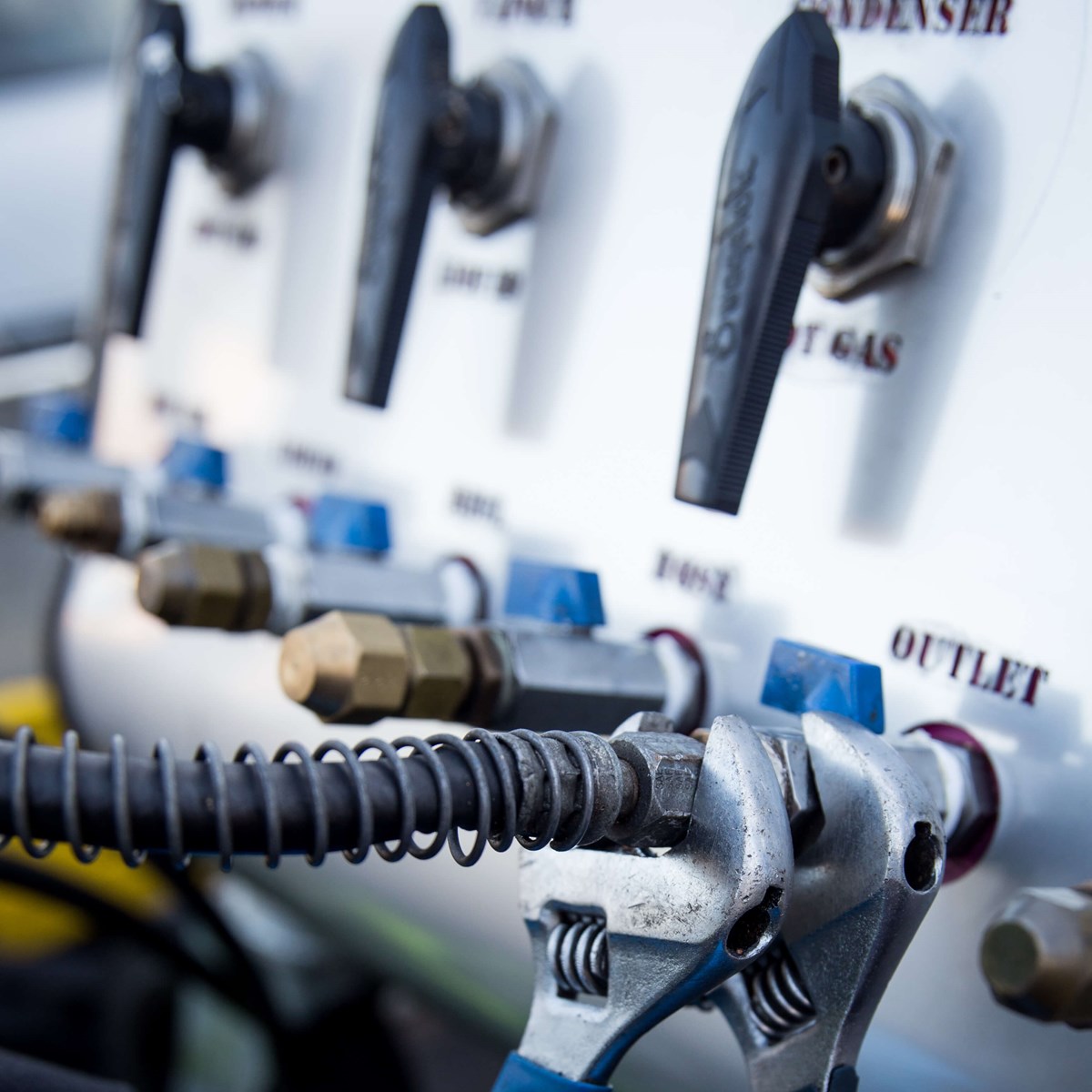
We capture the gas and vapour in the Rapid Recovery machine. Some jobs can take a little as two hours – while others can last as long as two weeks. Whatever the size of the job, we’ll stay on site for as long as it takes.
Awkward jobs are very much a speciality. In these cases contractors are unlikely to have the length of hose available to recover the gas. If a supermarket pack is on a roof or tucked away in an inaccessible corner you need long hoses to match. Our lines can reach up to 100 metres and with the mobile nature of Rapid Recovery this gives us much versatility. We can recover any volume of gas and on one occasion have removed as much as seven tonnes from a single site. We’ll keep going until the job is done.
Typically, we can recover 100 kilos in two hours. This work could take a contractor up to two days to complete.
In instances where the contractor wants the refrigerant removed from the system to allow them to carry out a repair, and then return the gas to the system, our recovery team can also help. The contractor will not have to worry about providing receiver cylinders to store the refrigerant while the work is going on, our expert teams will take care of this including all aspects of the paperwork.
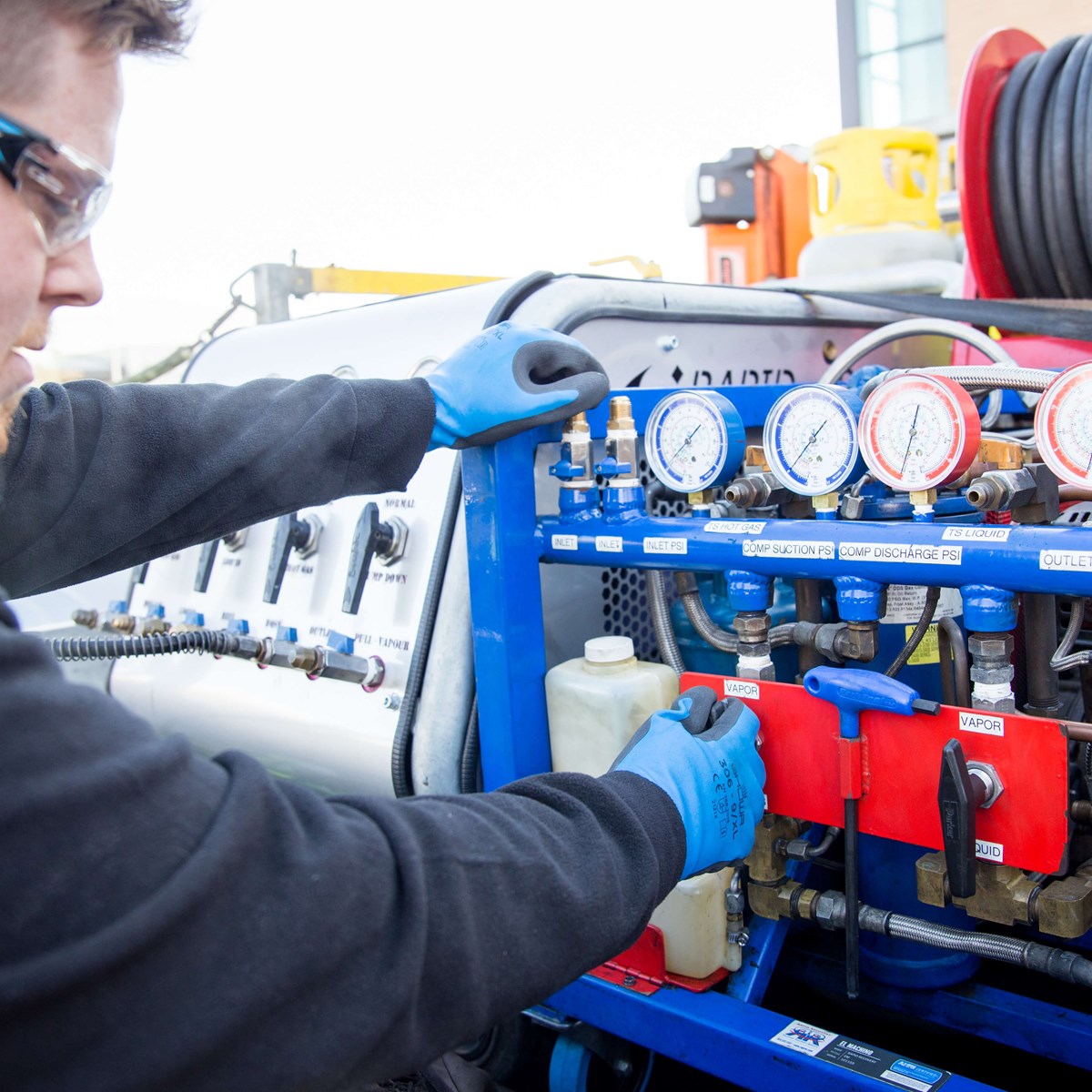
Compliance is important and we are often working in unregulated environments. We are regularly exposed to outside environmental risks like working at height. In other examples members of the public could be near to the site. We have to ensure all risk assessments are completed and the on-site safety policy is followed. In addition to this, we always ensure we are wearing the correct personal protective equipment.
The low GWP properties of flammable refrigerants mean that they are growing in popularity. A-Gas Rapid Recovery teams are fully ATEX trained and certificated to ensure that when we are removing flammable gases all is safe and sound. We can recover A2Ls like R32 using an ATEX-standard machine. Though risks associated with A2Ls are very low, we still have to take all the precautions necessary.
Many of our customers will keep the recovered refrigerant to use again, we will supply the cylinders to store the gas in. Hydrofluorocarbons (HFCs) are our main market at the moment, but if we are recovering older, banned high GWP gases like R12 or R22, we will take them away and destroy them in an environmentally-friendly way. HFC refrigerants contaminated with other gases can also be separated and used in other blends.
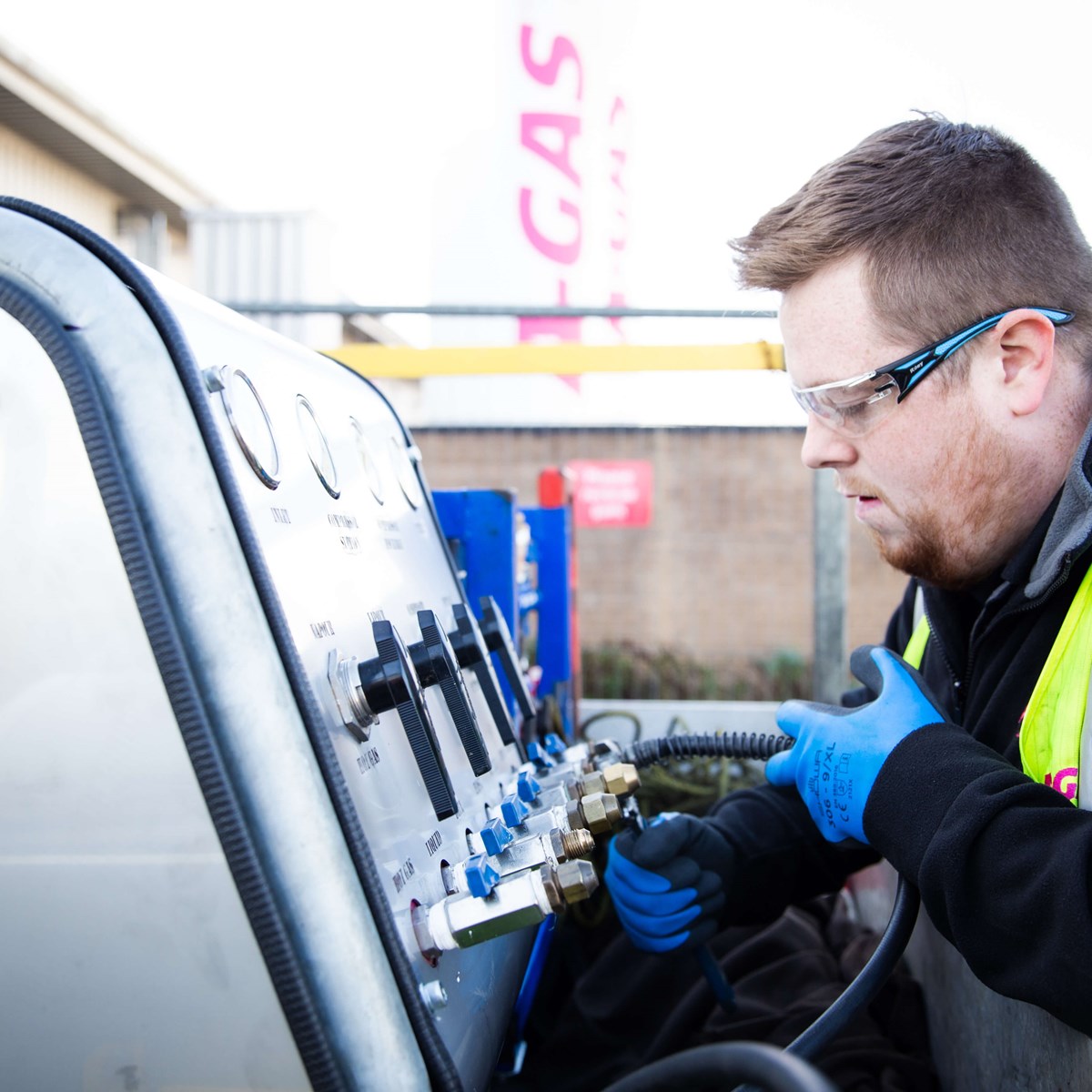
Gases containing oil, moisture and other impurities will also be taken away by our Rapid Recovery teams. Refrigerants sent to the A-Gas processing centres undergo chemical analysis, are cleaned of contaminants and passed through our reclamation and separation plant to create a product that matches the virgin specification. The refrigerant becomes fully reclaimed product and is returned to the market in line with the AHRI 700 standard.
Back on site when the job is complete, we leave the contractor with an F-Gas certificate to show that the refrigerant has been recovered correctly and to the letter of the law.
On-site bulk transfers of refrigerants are also an area we specialise in. Often, these gases are stored on behalf of equipment manufacturers and when large quantities of refrigerants need to be moved on site the time savings made by employing the services of Rapid Recovery are substantial.
Typically, with a recovery job we are dealing directly with the contractor. Decommissioning equipment is an area of the market where we can be called upon. We recently tackled a job at an old factory where there were more than 100 old air conditioning units and a number of large chillers scattered around the site. All the refrigerant had to be removed so there was a lot of R134 and R410A to be recovered.
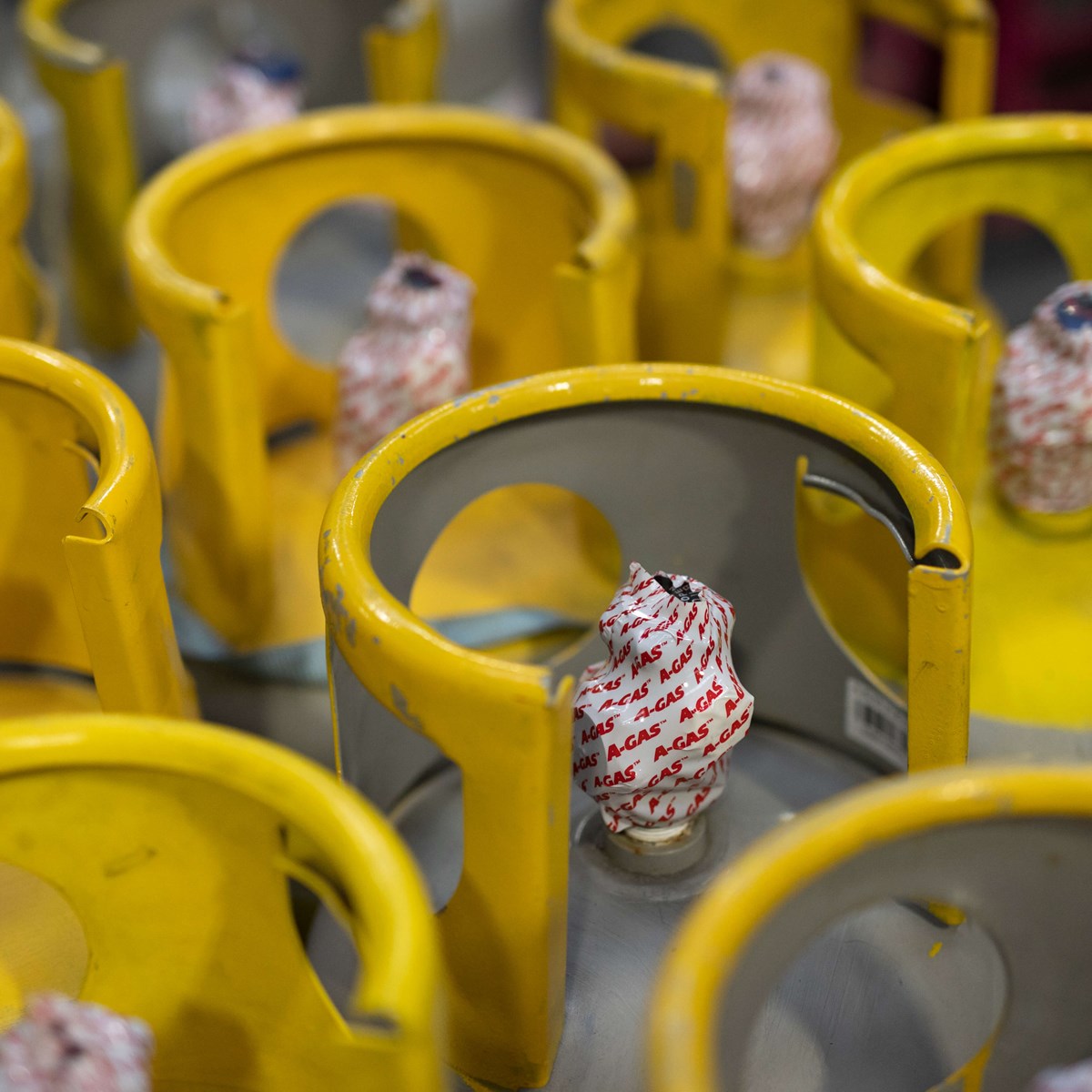
You can be sure that the role of refrigerant recovery and re-use will grow in future. As long as the gases are re-used and not emitted into the atmosphere they are not harming the planet. Recovery also removes any temptation for rogue contractors to destroy the gases illegally.
Refrigerant recovery and re-use is not only good for the environment but it is also good for business. It highlights how businesses with low carbon policies at heart can not only save time and money but also show to their customers in a practical way that they really do care for the planet.
Get in touch with our expert Rapid Recovery teams to find out how you can help build a more sustainable future.
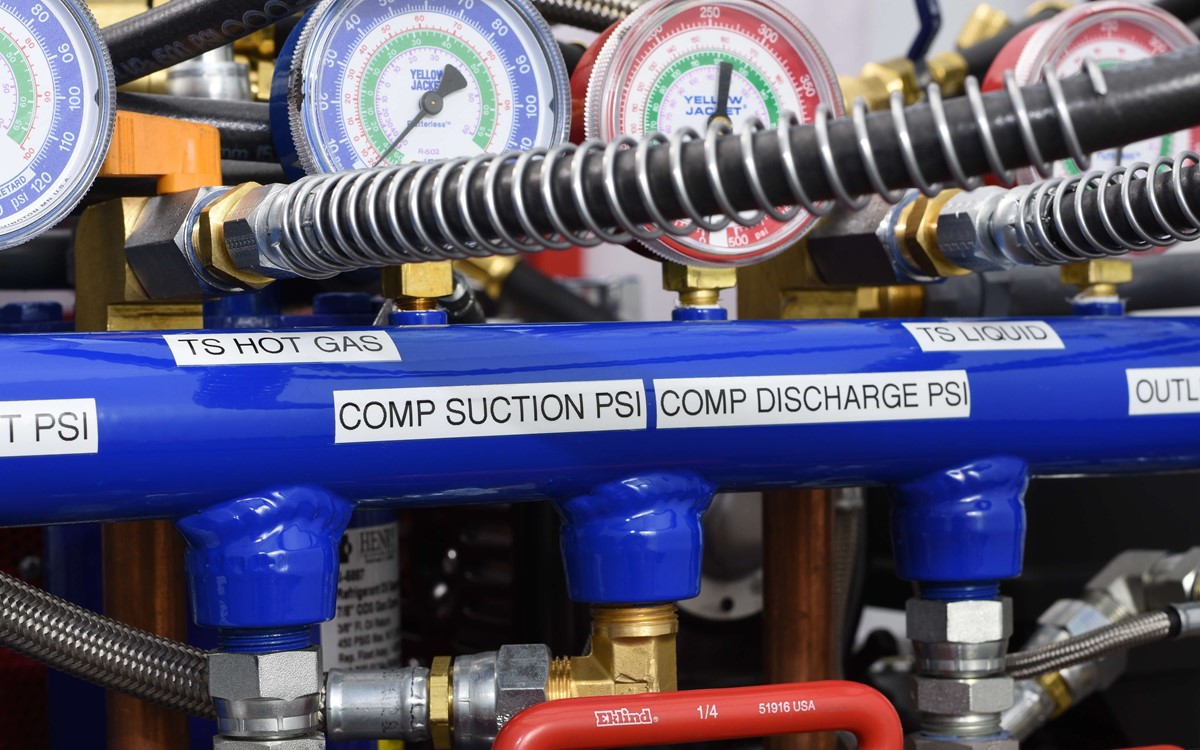
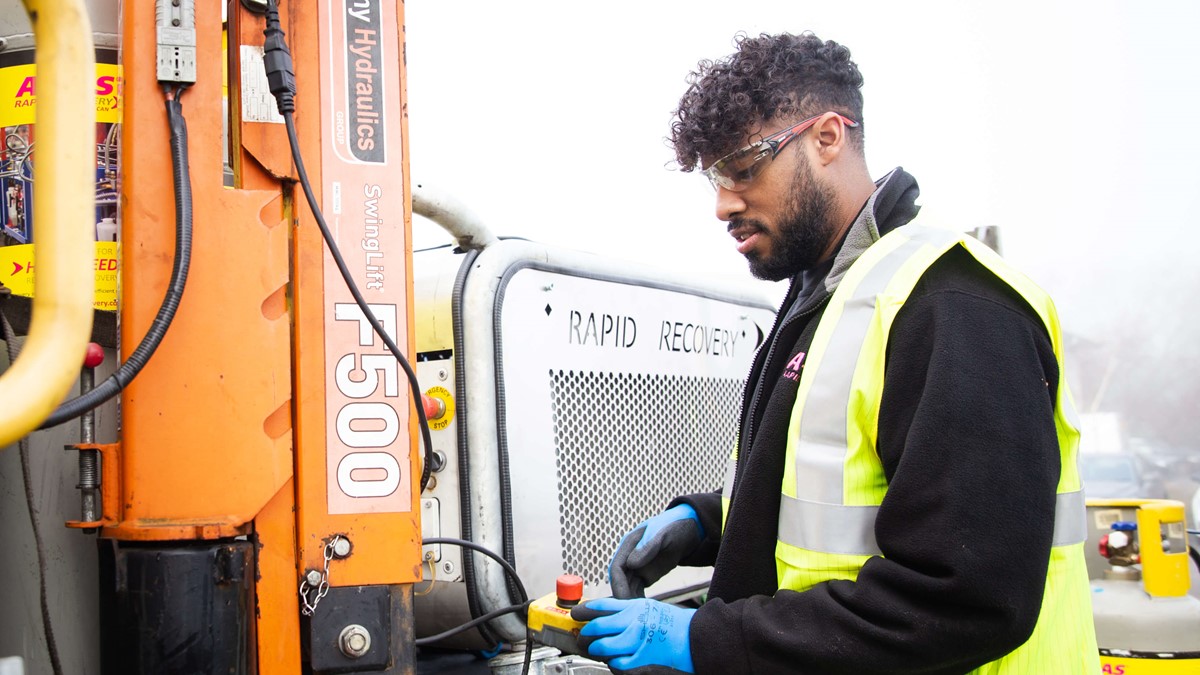